Smart Manufacturing: Where Physical Meets Digital with Intelligent 3D Replicas
Imagine your entire manufacturing operation—every machine, process, and workflow—perfectly replicated in a dynamic 3D environment that updates in real time. This digital counterpart doesn't just mirror your factory; it predicts equipment failures before they happen, identifies bottlenecks before they form, and simulates process improvements before you invest a single dollar in physical changes.
This isn't a far off distant future technology. Manufacturing leaders are implementing digital twins today, creating comprehensive virtual replicas that transform how industrial facilities operate, maintain equipment, and ensure worker safety.
Why Digital Twins Are Becoming Essential for Manufacturing Success
Traditional manufacturing relies heavily on reactive approaches fixing problems after they occur, addressing inefficiencies after they impact production, and improving safety protocols after incidents happen. This reactive cycle costs manufacturers millions in downtime, creates unpredictable production schedules, and puts both equipment and personnel at unnecessary risk.
Digital twins fundamentally change this paradigm by enabling prediction, prevention, and optimization through real time virtual monitoring. The result? Dramatically reduced downtime, optimized equipment performance, and safer working environments.
Three Game Changing Applications Transforming Manufacturing Today
1. Predictive Maintenance: Eliminating Costly Downtime
The Challenge: Manufacturing plants need constant monitoring to prevent machine failures, optimize workflow efficiency, and reduce maintenance costs.
Digital twins solve this challenge by creating virtual replicas of factory floors and production lines in real time, detecting inefficiencies, predicting equipment failures, and ensuring seamless operations.
Real World Success: Boeing has transformed aerospace manufacturing by implementing digital twins across its production facilities. These comprehensive virtual models simulate assembly lines, monitor equipment performance, and predict maintenance needs with remarkable precision.
Boeing's digital twin of the T 7A Red Hawk assembly line enabled engineers to simulate and optimize every step before physical build out, resulting in an 80% reduction in assembly hours, a 50% reduction in software development and verification time, and a 75% increase in first time engineering quality, thereby minimizing rework and scrap.
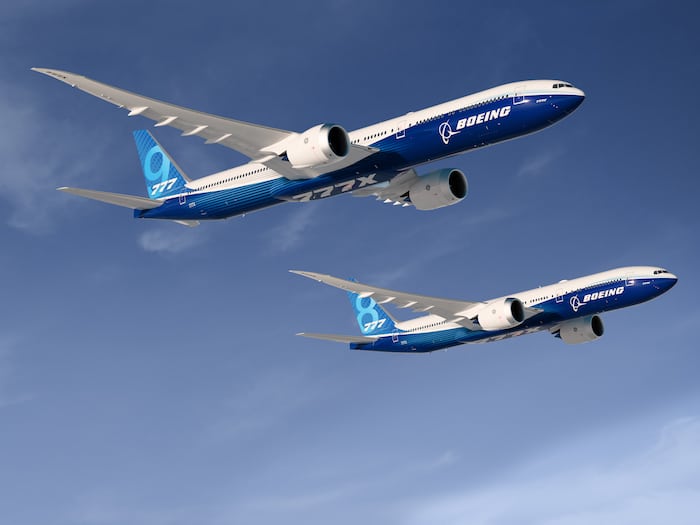
2. Smart Logistics & Warehouse Management: Streamlining Supply Chains
Manufacturing excellence extends beyond production lines into warehousing and logistics. Digital twins are revolutionizing these critical areas by optimizing space utilization, inventory management, and order fulfillment processes.
By creating detailed 3D models of warehouse environments, manufacturers can test different layouts, simulate picking routes, and analyze traffic patterns before implementing physical changes.
Transformation in Action: DHL has pioneered the use of digital twins in logistics operations. Their smart warehouses leverage digital replicas to optimize inventory placement, streamline picking routes, and forecast demand patterns with unprecedented accuracy.
Also, AWS's IoT TwinMaker powered InterlakeMecalux's fulfillment center digital twin, allowing them to test pick and put away workflows and storage layouts before making any physical changes; they achieved a 40% boost in labor productivity, a 15% improvement in overall space utilization, and 99.9% inventory bin accuracy through automated cycle counting simulations
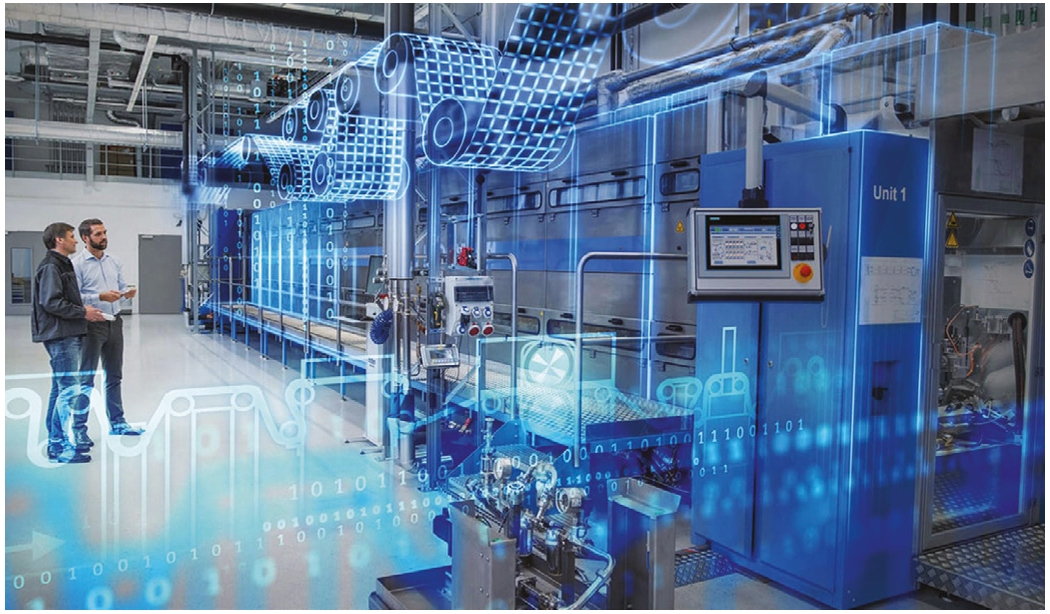
3. Enhanced Work Environment: The Future of Training
Manufacturing environments present inherent safety challenges. Digital twins provide revolutionary approaches to mitigating risks through virtual simulation, immersive training, and predictive hazard identification.
Setting New Standards: Siemens has established itself as a leader in leveraging digital twins for safety applications. Their comprehensive facility models simulate operational scenarios, identify potential hazards before they cause incidents, and provide immersive virtual training environments that prepare workers for complex or dangerous tasks.
Also, digital twin powered VR simulations are transforming safety training: in recent pilot programs, immersive, scenario based training delivered via a digital factory twin achieved a 70% improvement in training effectiveness—measured by knowledge retention and response time—and a 45% reduction in actual workplace accidents among participants .
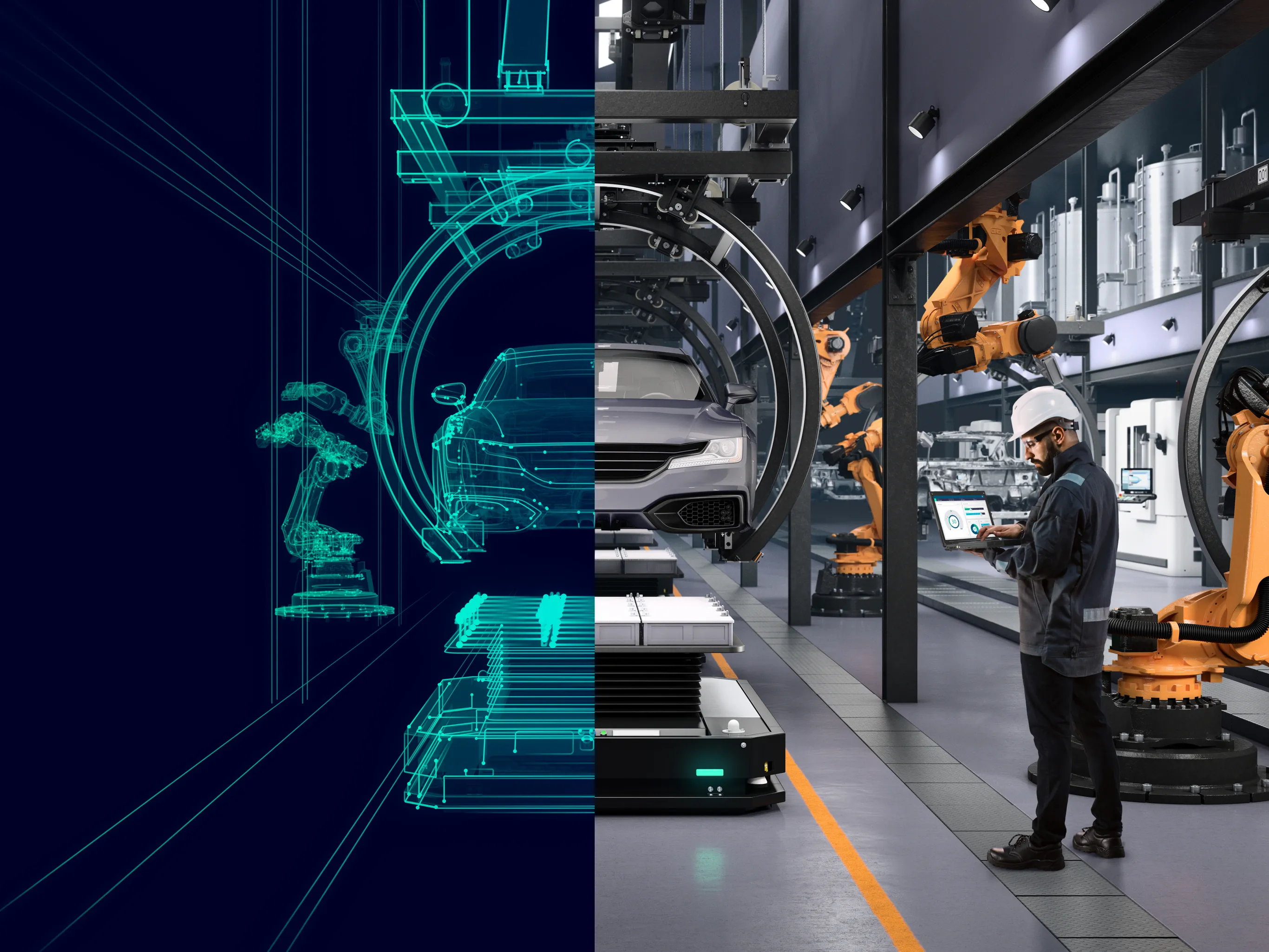
Building Manufacturing Resilience Through Digital Innovation
Digital twins represent a strategic approach to operational improvement that delivers measurable ROI while minimizing capital expenditure. By testing changes virtually before physical implementation, companies can reduce risk and maximize the impact of limited resources.
As global competition intensifies and markets remain unpredictable, digital twins provide a path to operational resilience and cost effective optimization. Forward thinking manufacturers are implementing these technologies to create decisive advantages to prepare for tomorrow. Digital twins deliver measurable business outcomes through enhanced operational efficiency, reduced downtime, and improved worker safety—critical factors for maintaining competitiveness in challenging times.
Ready to explore how 3D digital twins could help your manufacturing operation navigate today's challenges? Let's start a conversation about how to optimize for tomorrow.
Learn more about Wavefront 3D Digital Twins and connect with us today.